- Fireplaces and Wood Stoves
- Basic Fireplace Types
- How to Build a Real Wood Fire
- Fireplace Draft Problems
- Fireplace Cleaning
- Rain in the Fireplace
- Wood Stoves
- Whirlpool Bath
- Hot Tub,Spa
- Swimming Pools
- Pool Safety
- Waterfront Property and Seawalls
Fireplaces and Wood Stoves
Before modern heating sources were available, fireplaces were a primary source of heating. Today a fireplace can’t compete with a modern heating system. Fireplaces and wood stoves are great fun and provide a cozy, romantic amenity to our homes, but you do need to understand their basic components and how they operate.
Poor maintenance and improper operation can cause a fire inside your home. Fireplaces and wood stoves can produce dangerous products of combustion, such as carbon monoxide.
Basic Fireplace Types
There are three basic types of fireplaces: masonry, prefabricated metal and direct vent. Masonry fireplaces are designed to burn wood and can be adapted for a gas log set. Prefabricated metal fireplaces can be designed to burn wood, wood and gas, or just gas. Direct vent fireplaces are sealed high-efficiency units that only burn gas. We will look at each type and learn what’s involved in safe operation.
A wood stove or fireplace insert should not be operated until a professional has checked it and determined that it conforms to local building codes and requirements. If you have any concerns or specific questions about your fireplace or wood stove, contact a local member of the Chimney Safety Institute of America (CSIA). Local fireplace and wood stove dealers can also provide assistance.
Masonry Fireplace
Masonry fireplaces have been the standard method of home heating for centuries. Since about 1900, when efficient central heating systems were developed, fireplaces have taken on the role of a desirable feature that adds value to our homes and provides a gathering place for family and friends.
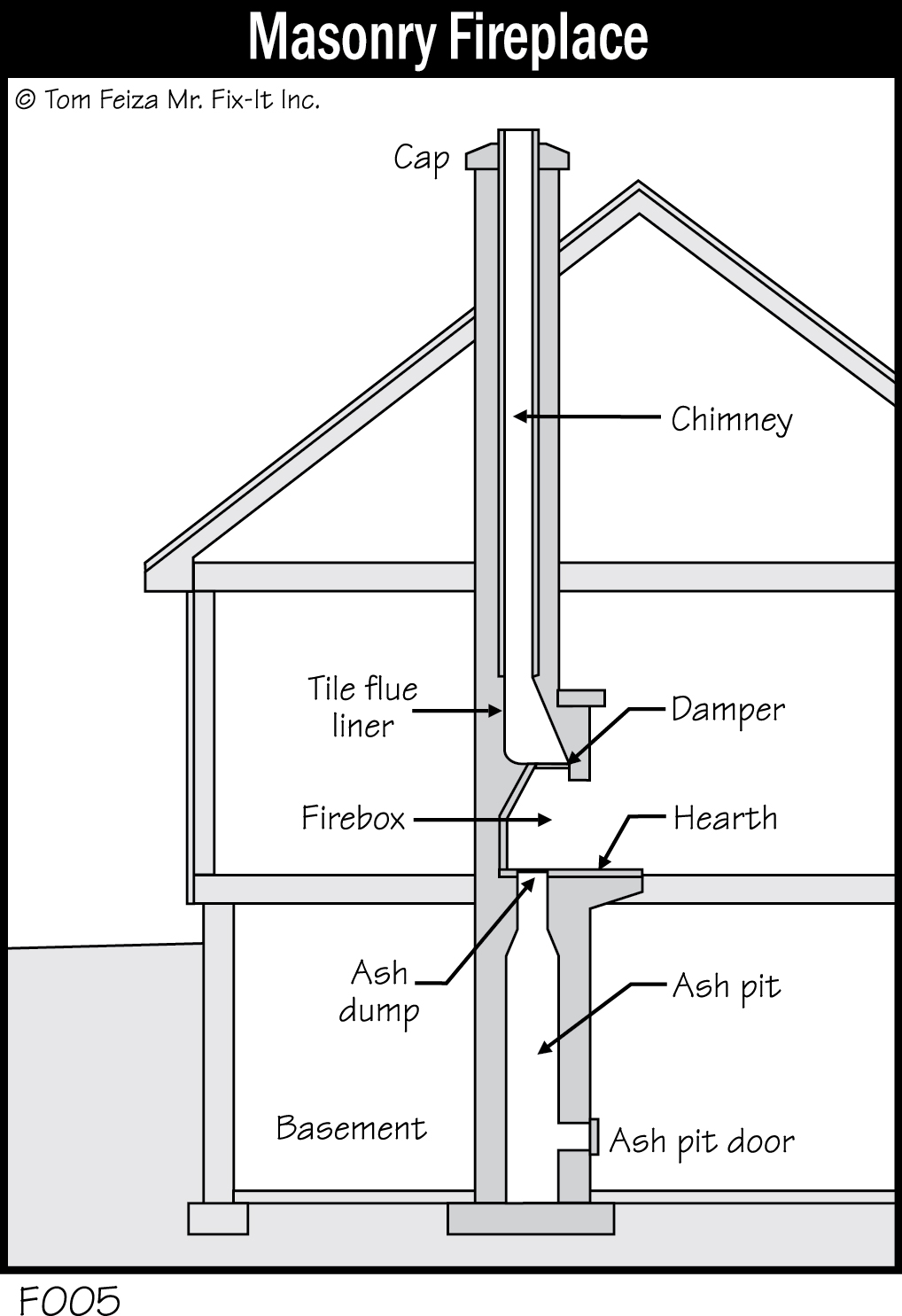
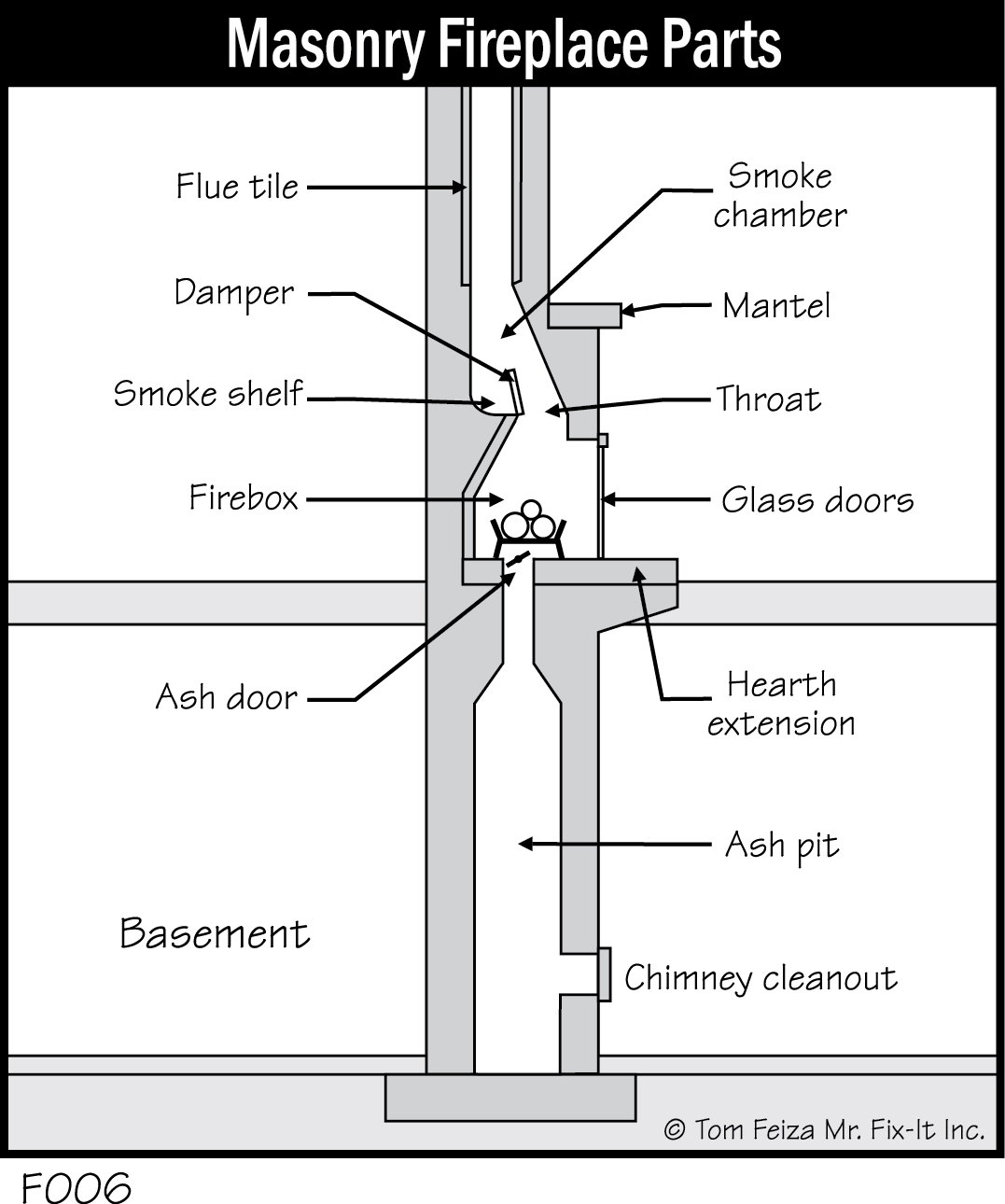
A standard masonry fireplace is constructed of brick, firebrick, cement block and clay tile to contain the fire and products of combustion. The fireplace is custom built on-site by skilled masons. The design has changed little over the last 100 years, and masonry fireplaces aren’t a very efficient source of heat.
Before you build a fire, you should understand the components of your masonry fireplace. Start by examining the firebox (the area where the fire is built). You will notice that the box is built of smooth brick or firebrick. If the wall of the firebox is metal, you have a metal framed or metal fabricated fireplace.
Look inside the top of the firebox and you will see a metal damper (metal plate) and a handle that operates the damper. Most dampers are made of cast iron and are pushed open with a handle or pulled open with a chain. With the chain-operated units you will often see a pull marked “O” for open and “S” for shut. Pull the chain or push the lever to open the damper. Keep your face and body away from the damper as it opens, because soot may fall from the opening.
With the damper open, you should be able to peer up the clay tile flue and see part of the way up the chimney. You may notice some sootand tan-colored fluff or deposit. This is creosote. If you see a heavy buildup that is 1/16” to 1/4” thick, have your chimney and fireplace cleaned before you build a fire.
When you build a fire, the hot gases of combustion flow past the damper and up the chimney flue. The firebrick and firebox contain the heat of the fire and radiate some heat back into the room.
A variation on a solid masonry fireplace uses a metal firebox placed inside a masonry fireplace frame. The metal firebox replaces the firebox constructed of firebrick. These units often were constructed with an air passage around the metal box and air duct connections to the room. The lower duct opening draws air from the room at the base of the fireplace. The metal firebox warms the air, which then flows upward through a duct above the fireplace and enters the room through a grill. This gives the fireplace some heating capacity, warming the air of the room.
You might also find a wood-burning metal stove insert fitted inside a masonry fireplace. These custom-designed units provide heat to a room. Often, such a unit has a partially sealed combustion chamber. It requires a special flue and custom installation. This kind of unit needs yearly maintenance; flue gases exit at a lower temperature, and the unit is prone to a buildup of deposits in the stove and chimney flue.
Metal-Framed Prefabricated Fireplace
Many fireplaces built since about 1970 consist of a metal fireplace and flue built in a factory, which is then installed in a wood frame inside the home. These are called metal-framed, zero clearance, prefabricated, or factory-built fireplaces. They are designed and tested as a unit. Don’t be confused by a solid brick or masonry front and mantle on such a fireplace; many metal fireplaces have a masonry front.
If yours is a factory-built fireplace, you will see a metal firebox with refractory panel liners, metal damper and a metal flue. The refractory panels will look like brick cast into a flat panel on three sides of the firebox. The side of the firebox may show the manufacturer’s data and nameplate. Outside the house, there will not be a brick chimney; instead, you will see a wood-framed chimney chase and a metal-capped flue pipe. The flue or discharge pipe at the top of the chimney will be metal. The chase can also be covered with masonry materials, but this is not common.
A prefabricated fireplace functions like a masonry fireplace but doesn’t require the foundation and more expensive masonry construction. Glass doors are often included with the firebox, and the fireplace may have an outside air supply that provides combustion air for the fire. This reduces the need for inside air for combustion and makes the fireplace more efficient.
Many prefabricated fireplaces are equipped with a fan to circulate room air around the firebox so that the fire provides some heat in the room. The grills for air circulation are often placed directly above and below the glass doors.
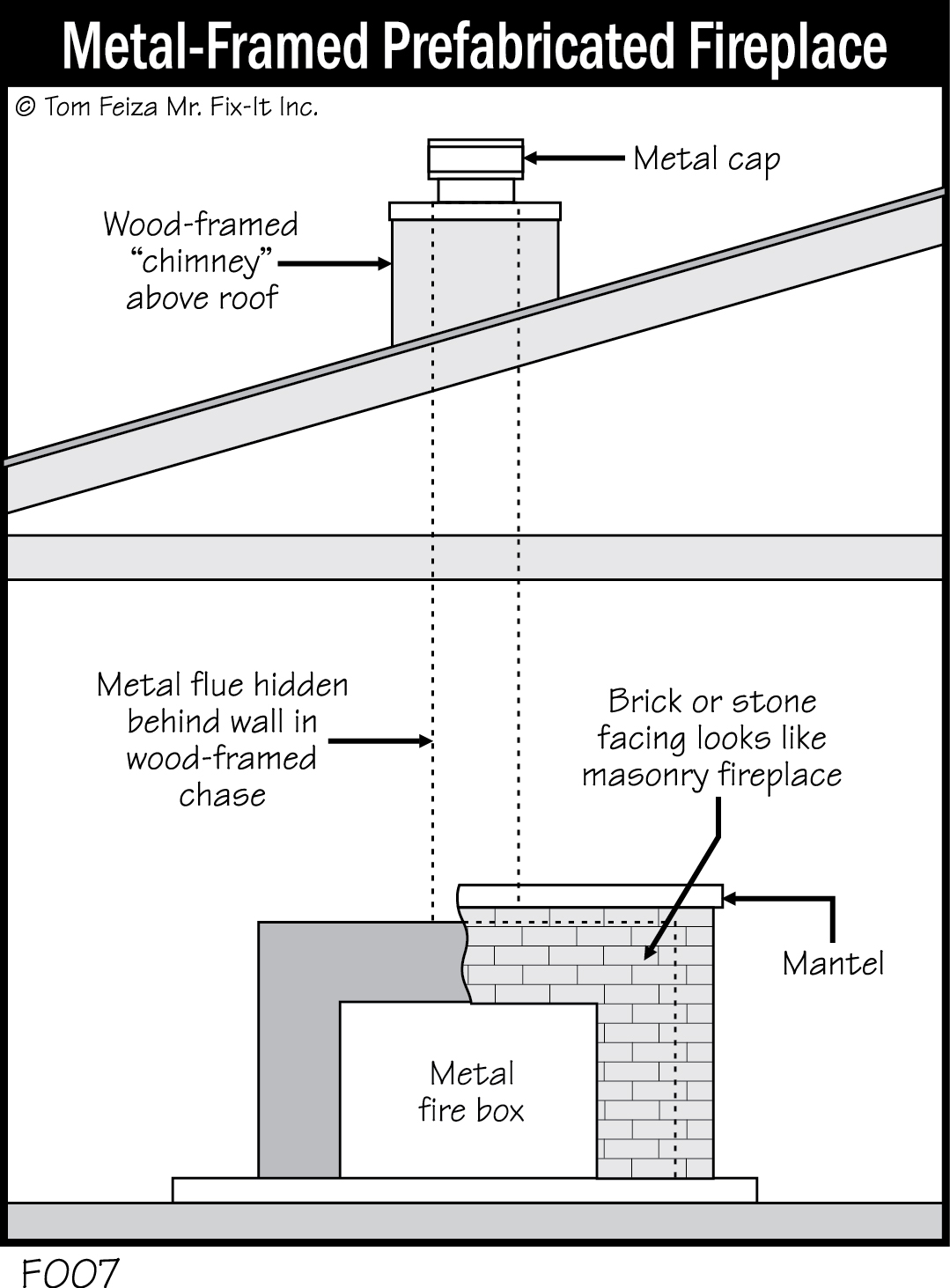
Direct Vent Fireplace
Around 1985, fireplaces were greatly improved as heating appliances when “direct vent” and “sealed combustion” fireplaces started to become popular. These are natural gas or propane burning fireplaces that vent combustion gases directly through a sidewall or up a special metal chimney. They use an outside air supply for combustion. The front glass is totally sealed.
This fireplace may have a pilot light or ignition device, just like a gas furnace. With a good set of gas logs, it provides an attractive flame and is an efficient source of heat. Some of these units are rated heating appliances, just like a warm air furnace, and can be connected to a thermostat for automatic control. The fireplace will have a fan to circulate heated air into the room. Many units are almost as efficient at heating the room as a good warm-air furnace.
A “gas” fireplace generally refers to a set of ceramic logs, a gas burner, and related equipment that allows the feel and look of a real fire while burning natural gas or propane. The advantages of a gas fireplace are that it requires no fuss and creates no mess. You can have an instant fire, and when you turn it off, you know the fire is out. There is no wood to haul in and no ash to clean up.
Gas fireplace logs are often adapted to a woodburning masonry fireplace or to a metal-framed fireplace that is designed to burn wood.
Since each system is a little different, refer to the manufacturer’s instructions for your unit. Some will have a pilot light or an automatic ignition device. Some use a wall switch or even a remote control.
With most manually operated gas fireplace logs, the first step is to open the damper in the flue above the logs. Then you place a match or flame in the log set. Use a long fireplace match or a lighter with a long handle. Carefully and slowly open the gas valve after there is a flame in the log set.
If you smell gas near the gas fireplace, do not attempt to light the unit. Turn off the gas valve located in the floor or in the firebox near the log set. Call for service. There should also be another safety valve in the basement or near the fireplace.
If you intend to burn real wood in a gas fireplace, consult a specialist first. Some metal-framed fireplaces are rated for gas only and won’t burn wood. If your unit has a gas log set and gas piping, it would be very dangerous to burn real wood without converting the unit.
How to Build a Real Wood Fire
Masonry fireplaces and wood burning metal-framed fireplaces are safe and easy to use if you follow a few simple steps.
First, get everything ready:
- Assemble a simple set of tools for maintaining the fire. At a minimum, you need some type of poker to move logs as needed when the fire is hot.
- Always use a grate in the fireplace. The grate raises the wood off the base of the firebox to allow for air circulation, which aids complete combustion. Place the grate to the rear of the firebox.
- Use dry or seasoned hardwood. This wood will burn hotter and prevent excessive smoke and soot from building up in the chimney flue. Dry or seasoned wood will have been cut and stored out of the weather for about 12 months. It will feel dry and will have cracks and splits in the end grain.
- Never burn treated wood, Christmas trees, plastic, or trash in a fireplace. Never use a flammable liquid.
- Remove ashes as they build up below the grate. There must be room for air circulation below the grate. If yours is a real masonry fireplace, you can put cold ashes down the ash pit door. Leave a base layer of about one inch of ash in the fireplace.
Now, to build the fire:
- Open the damper. Take a look up the flue with a flashlight to make sure the damper is open. (Once you have mastered the operation of the damper, you can stop checking with the flashlight.)
- If your home is very “tight,” you may need to open a window to allow for combustion air to reach the fire. You will learn about this as you use the fireplace; if there is a poor draft, or if smoke builds inside your home, try opening a window.
- Start loading the fireplace with small pieces of scrap wood (kindling) on the grate. Using small pieces of dry wood for kindling is the key. Woodworking scraps are ideal. These will light quickly, spreading the fire easily to the logs.
- Add three or four small logs in the grate atop the kindling. Arrange the logs so there is space for air and fire circulation between them.
- Place wadded newspaper below the grate.
- You may need to help start the draft with a torch made from rolled newspaper. Light the paper and hold it up near the damper until there is a strong draft. The flame will warm the air in the flue and start a draft (a draw) up the chimney. After you have burned a few fires, you will know whether you can skip this step.
- Once there is a draft up the chimney, light the crumpled paper below the grate.
- Keep the screen closed while you are burning a fire.
- Add and move the logs if needed. Don’t build a huge fire.
- Monitor the fire as it burns. Allow it to burn out before you leave the room. If your fireplace has glass doors, close them when you leave the fire.
- Don’t close the damper until the next day, and make sure the grate and remnants of logs are totally cold. A wood fire can smolder for a long time, and if you close the damper when the fire is still burning, you will trap smoke and dangerous products of combustion inside your home.
Must Know / Must Do Building a Fire
- Keep the damper open overnight after burning a wood fire.
- Routinely have the fireplace and flue cleaned by a professional.
- Watch for soot and creosote buildup.
- Consider glass doors; they’re a great addition to your fireplace. They contain the fire and help prevent excessive room air from entering the fireplace.
- Never light a gas fireplace if you smell gas. Treat this as a serious safety hazard.
- If you see cracks, crumbling, or movement of the masonry surface inside the firebox or flue, have them checked by a professional.
- A professional should check excessive rust on a metal-framed fireplace.
- If you are not sure how to use your gas or wood-burning fireplace, get help from a professional.
Fireplace Draft Problems
One problem with fireplaces in newer, more airtight homes is that they lack combustion air unless a window is open. This was not a problem with older homes, which had so many air leaks around windows, doors and framing that there was plenty of air for combustion.
This condition can be dangerous: as a fire is starting or burning out, it may lack draft, and it can back up dangerous carbon monoxide into your home.
A fire with a strong draft can cause gas-fired appliances such as a water heater or furnace to backdraft combustion fumes into your home. Any gasburning appliance vented by gravity up a chimney could be affected. The draft of a fire can overcome the natural venting of these gas appliances.
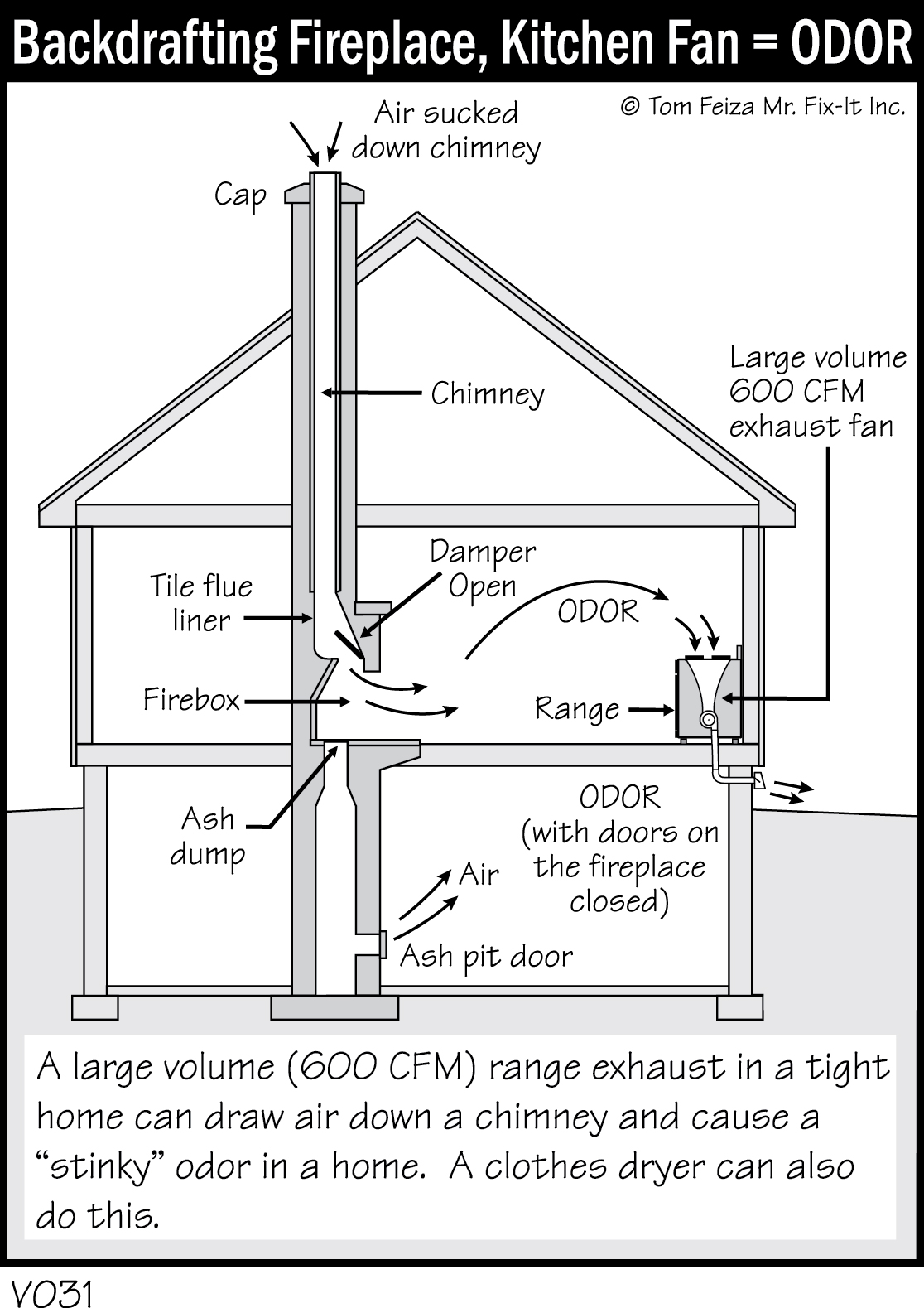
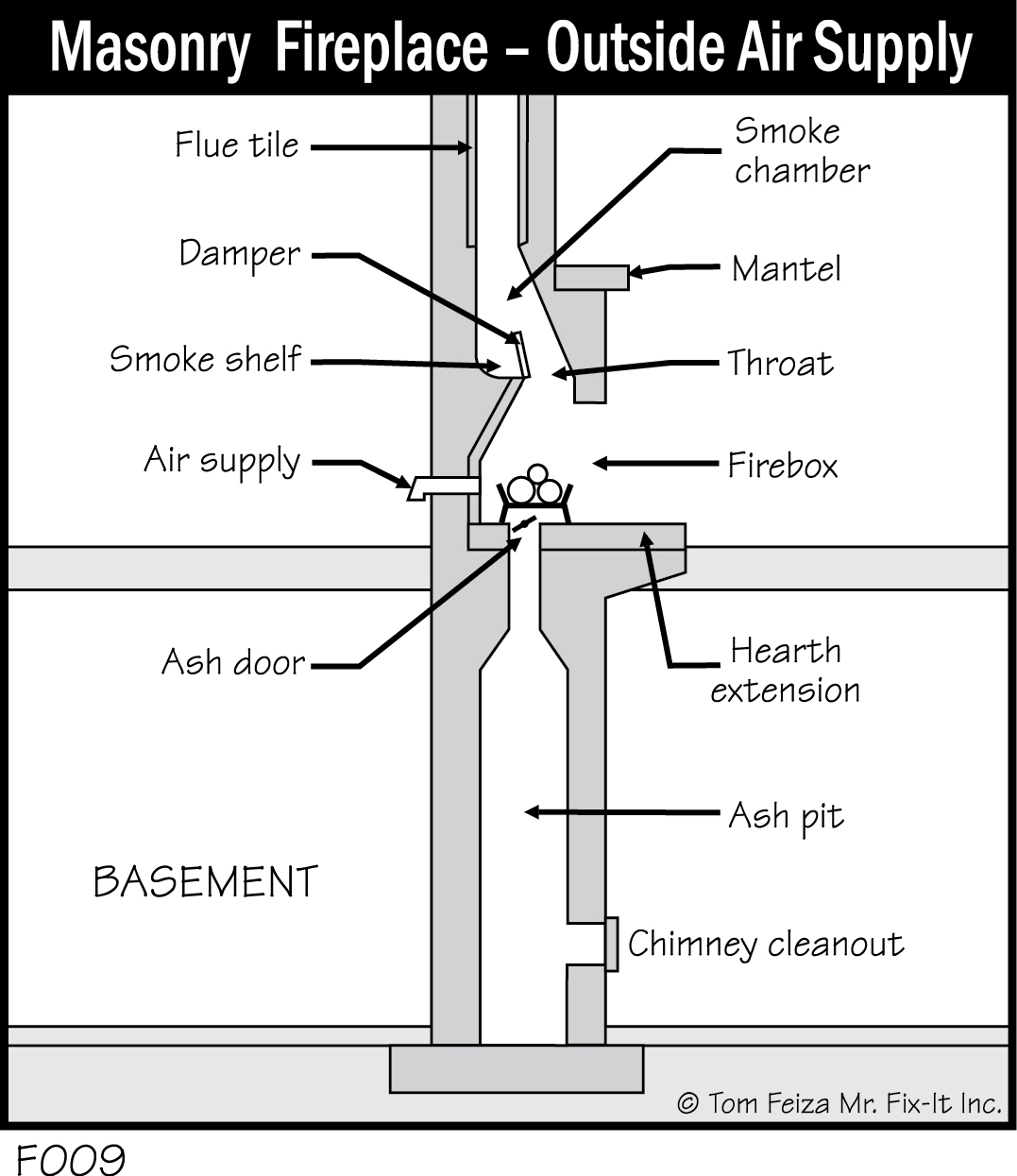
An air supply directed into the firebox would be a good solution. Consult a qualified brickmason, fireplace contractor or chimney sweep for the installation. This is definitely not a do-it-yourself project. The vent must penetrate an outside wall and the side or front of the fireplace. The vent may also need to be combined with fireplace doors.
Remember that when most natural fireplaces are operated in cold weather, most of the heat goes up the chimney.
There is one situation when a fireplace works well: if the home has excessive moisture levels in the winter, the fireplace will draw lots of air into your home for ventilation (provided that a window is open!)
Fireplace Cleaning
The ideal schedule for cleaning your fireplace and chimney depends on many factors. How often do you use your fireplace? What type of wood do you burn? Is the wood always dry hardwood? Is your home in a wooded area? Is there a cap on the chimney? Have you had problems in the past? Do you close the glass doors? Is there always a good draft? Is the chimney in the center of the home or on an outside wall?
If you live in a wooded area, you may wish to have the chimney checked every year just to make sure that no animals or their nests have blocked the flue.
You should inspect your fireplace, damper and flue every year. Operate the damper to see that it opens fully and latches open. The damper should also close tightly. Peer up the flue while shining a bright flashlight on it. You should not see any buildup of creosote or soot on the sides of the firebox or liner. The shelf behind the damper should not be full of debris. Proper inspection also includes looking at the top of the chimney, inspecting the cap, and peering down the flue with a bright light.
Creosote buildup creates a fire hazard. Creosote, a black or brown deposit, can be crusty and flaky, tar-like, or shiny and hardened. You might see different types of buildup on one fireplace. If creosote builds up in sufficient quantities, it can burn, destroying the chimney and even burning down your home.
Wet wood, restricted air for combustion, and cool chimney temperatures all increase the buildup of creosote, so no general rule of thumb can safely determine when a fireplace needs to be cleaned.
Have your fireplace cleaned, and ask the chimney sweep for recommendations on routine maintenance. He or she can determine how often your chimney needs cleaning, based on all the variables in your case. Select a sweep who belongs to the National Chimney Sweep Guild and is certified by the Chimney Safety Institute of America (CSIA). A chimney sweep must pass an examination to be certified. Remember that it’s the worker, not the company, who should be certified. To find the names of certified members in your area, call the CSIA at (317) 837-5362 (www.csia.org).
“Rain” in the Fireplace
To avoid severe condensation problems that mimic rain in the fireplace, check the fit of the fireplace damper. If the damper leaks (or is left open) during the winter, warm moist air will flow up the chimney. This warm air will condense into water on the flue if the chimney is cold from lack of use; when temperatures are below freezing, the condensation will turn to ice on the flue. When you build a fire, this ice can fall like “rain.”
“Rain” that falls onto your fire could also result from a leak in the flashing, a damaged cap, damaged brick and mortar, or a liner problem. If the problem persists, hire a certified chimney sweep to do an inspection.
Wood Stoves
Wood stoves, wood heaters, wood-burning fireplace inserts and related wood-burning devices have become popular over the years. Many are well-designed and safe to use. Some are homemade contraptions that are not safe. Some are excellent factory-built units installed by amateurs in an unsafe fashion.
If your home has any type of wood-burning device other than a professionally installed fireplace, have it checked by a professional before you use it. It may not be safe.
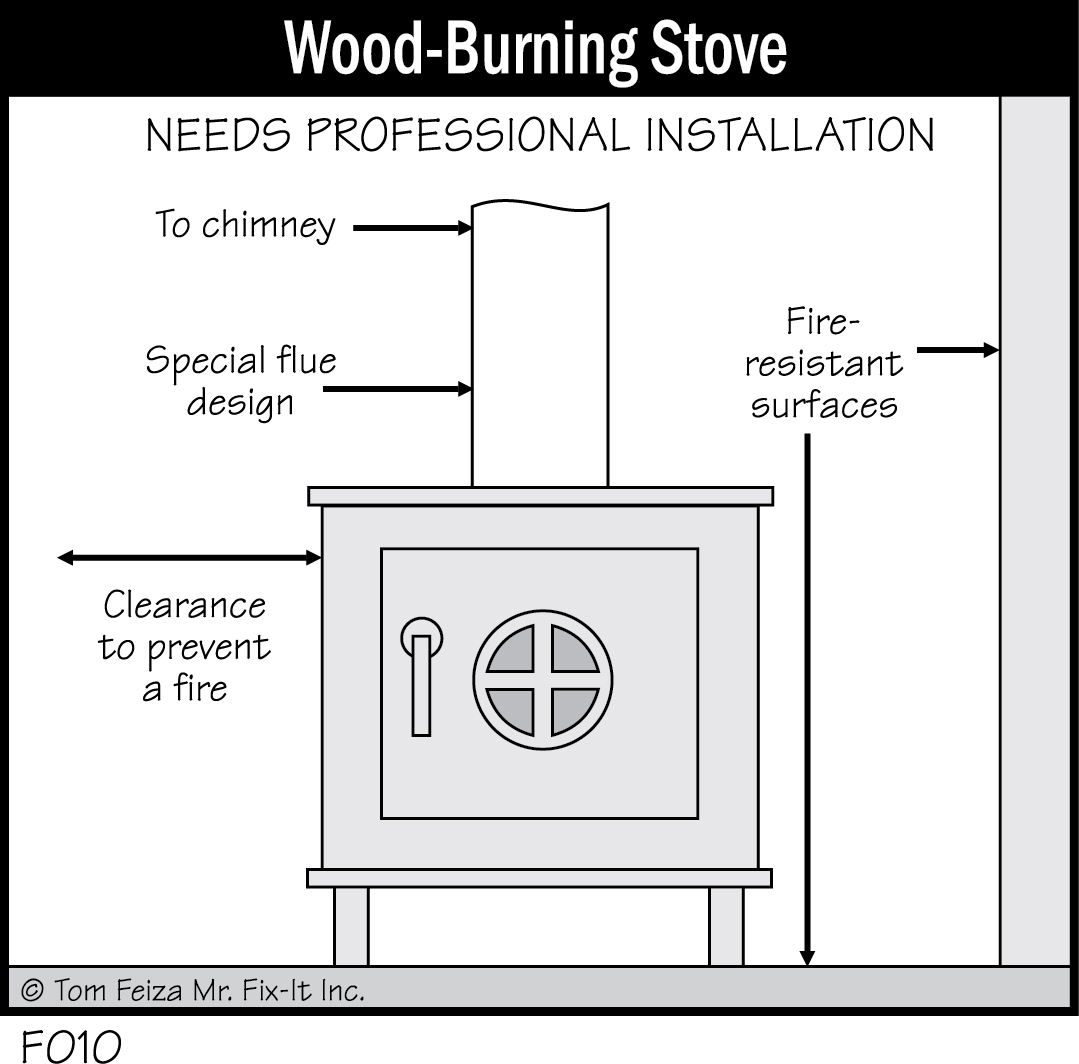
Whirlpool Bath
A whirlpool bath is a tub fitted with a circulating pump, jets, air induction, and possibly a heater. The tub can be small or large and is usually located in a bathroom. Most whirlpool tubs let you adjust the direction and amount of air in the jets for a more invigorating flow of water. Water is recirculated through the pump, the jets and a return opening.
The pump system usually is controlled by a switch on the side of the tub that uses pneumatic operation for safety. There may also be a timer and disconnect switch mounted on the wall away from the tub. The electrical system must be protected by a ground fault circuit interrupter (GFCI) outlet or breaker.
To use the tub, fill it with comfortably warm water to a level above the jets; then turn on the airflow to the jets, which should be pointed downward unless you want water spraying into your adjacent closet. You can adjust the jets to vary the amount and strength of the airflow. Adjust the temperature to your liking by adding more hot or cold water.
Whirlpool tubs should be flushed periodically, up to twice per month depending on usage. Debris can build up in the piping system if the unit is not used and flushed periodically.
The Kohler Co., a premier manufacturer of plumbing fixtures and whirlpool tubs, provides excellent information on whirlpool operation and maintenance information at its website, www.kohler.com. According to Kohler, whirlpool flushing should be done as follows:
- Adjust the jets fully clockwise so there is no air induction.
- Fill the bath with warm water to a level 2″ above the highest jets, or leave water in the bath after using.
- Add 2 teaspoons of a low-foaming dishwasher detergent and 20 ounces of household bleach (5 to 6 percent sodium hypochlorite) to the water.
- Run the whirlpool for 5 to 10 minutes. Then shut off the whirlpool and drain the water.
- If desired, rinse bath surfaces with water.
- Clean bath surfaces as needed with recommended cleaners.
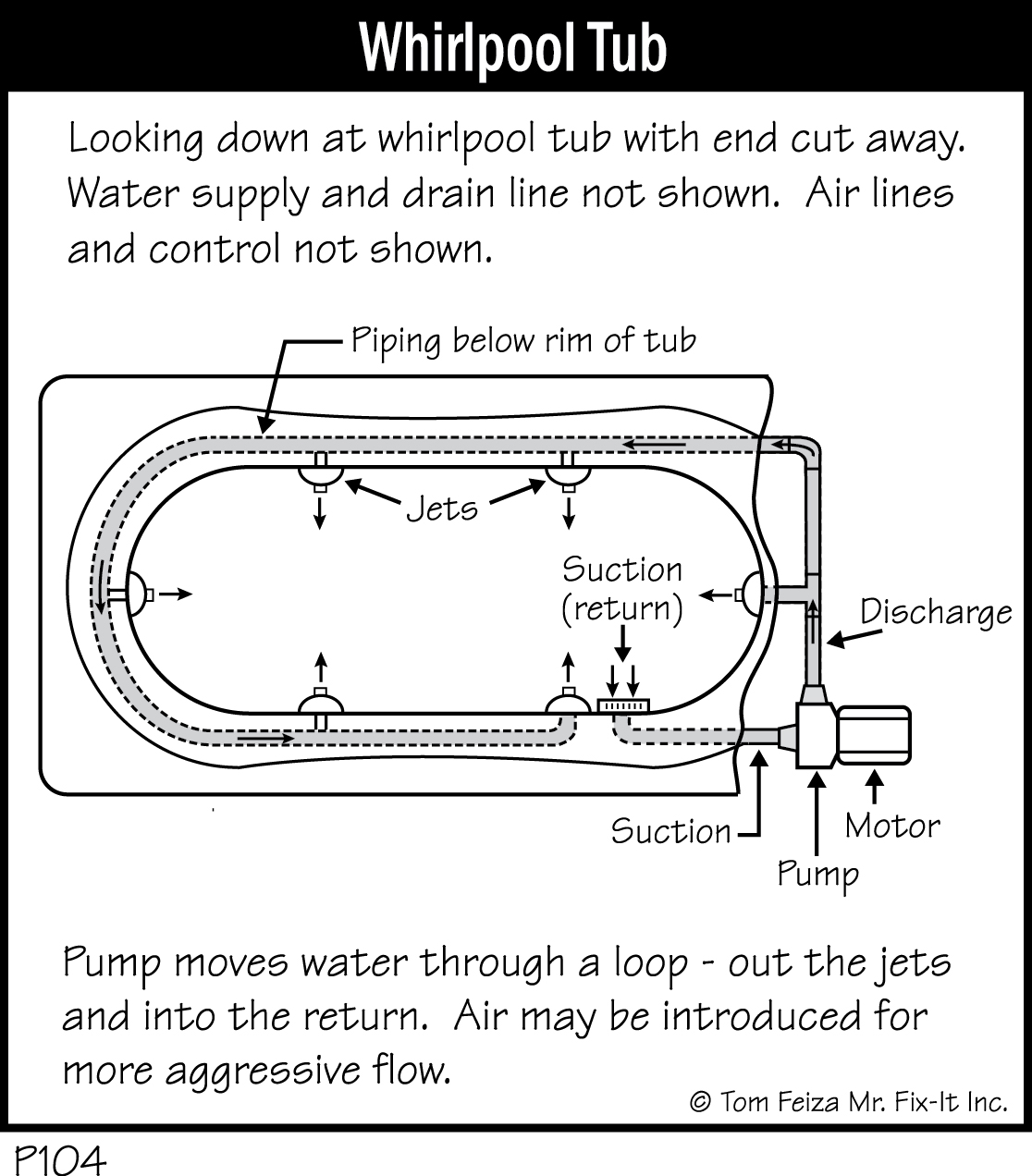
Must Know / Must Do Whirlpool Tubs
- Periodically flush and clean the unit.
- Test the GFCI routinely.
- Never use bubble bath or similar detergents.
- Never allow children to use the tub without supervision.
Hot Tub, Spa
Hot Tub/Spa A hot tub or a spa is a heated, water-filled tub that circulates water and often air through jets below the water line. Water is not drained from a hot tub as it is from a bathroom whirlpool tub.
The hot tub can be made of fiberglass, wood, acrylic or even poured concrete as part of a pool system. Hot tubs vary in size, shape, type and location. They have automatic controls and require routine maintenance.
A hot tub requires carefully controlled treatment with chemicals to maintain water quality. Ozone is also used to treat spa water. There are numerous methods for chemical treatment; some are manual and some are sophisticated, automated systems.
Self-contained (sometimes called portable) spas include the tub and all related equipment—heater pump, jets, filter, air system and automatic controls. They may also include some type of automatic chemical treatment. Usually the heater is electrical and the unit requires a large 240-volt electrical service with ground fault circuit interrupter (GFCI) protection. In most climates these tubs are fitted with a cover to conserve energy and water and maintain the chemical balance. Automatic controls maintain the temperature and operate pumps and heaters.
An in-ground spa installed with a pool usually has a separate pump, filter, heater, air system and chemical treatment. The equipment is often located outside but can be located in a pool room or basement. The heater for this type of spa is usually gas- fired—basically, it’s a small gas boiler.
You may wish to hire a contractor for routine maintenance and chemical treatment. The chemicals and equipment must be carefully controlled to provide a safe system and to prevent equipment damage.
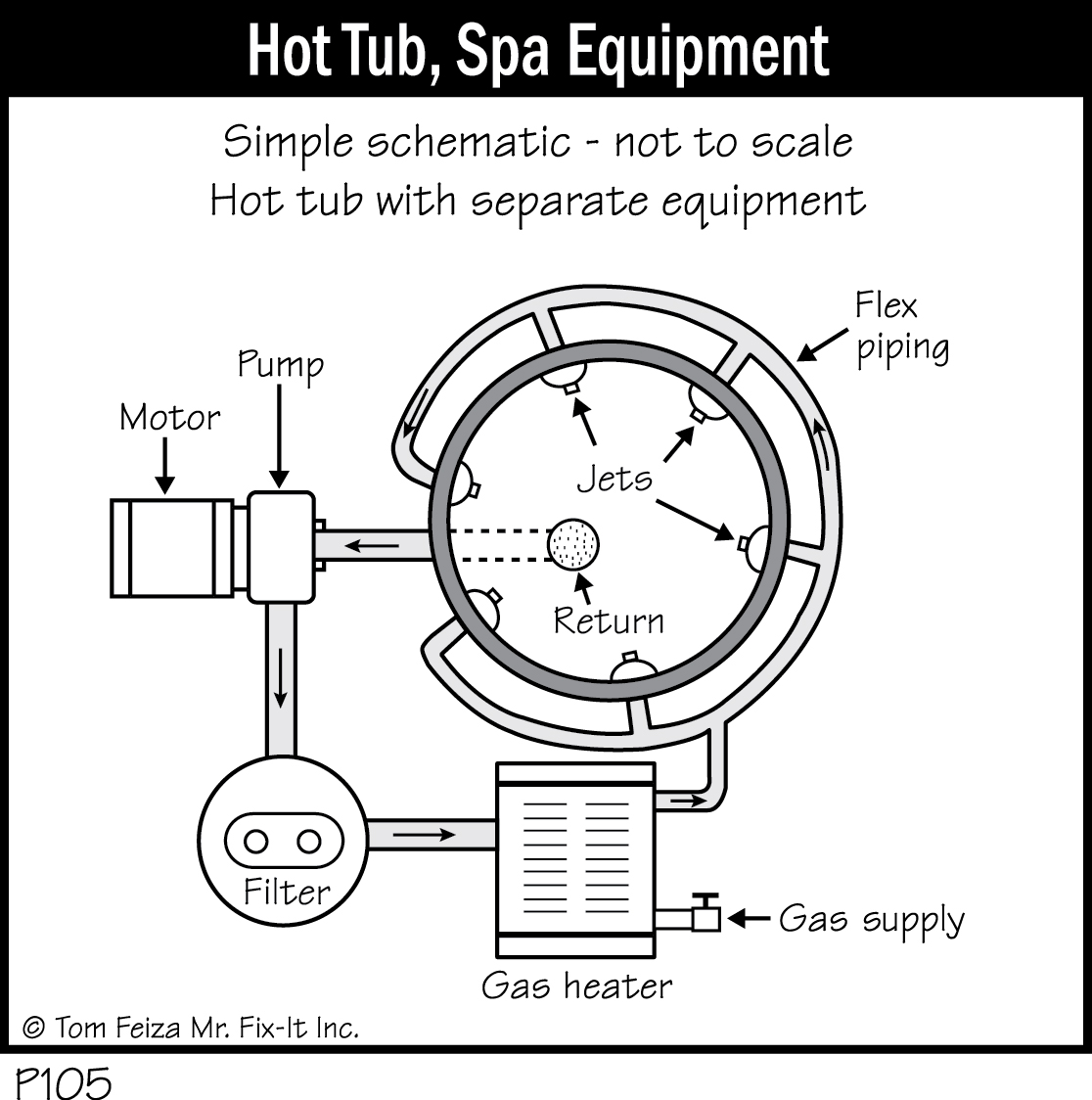
Must Know / Must Do Hot Tubs and Spas
- Maintain water quality through chemical treatment.
- Keep covered to control water and chemical loss.
- Periodically flush and clean the unit. Test the GFCI routinely.
- Never use bubble bath or similar detergents.
- Never allow children to use the hot tub without supervision.
- Watch for leaks.
- Listen for unusual equipment noises.
Swimming Pools
A swimming pool is a man-made tub of water designed for recreation, exercise, and staying cool on a hot summer day. Swimming pools come in all types, shapes and sizes. Some are above ground, some below. Most of them share common systems and components.
Most pools include a pump, filter, strainer, skimmer, drain, valves, and piping that connects all these components. In addition, a pool may have a heater, lights and an automatic treatment system. The treatment may be chemical, salt or oxygenation.
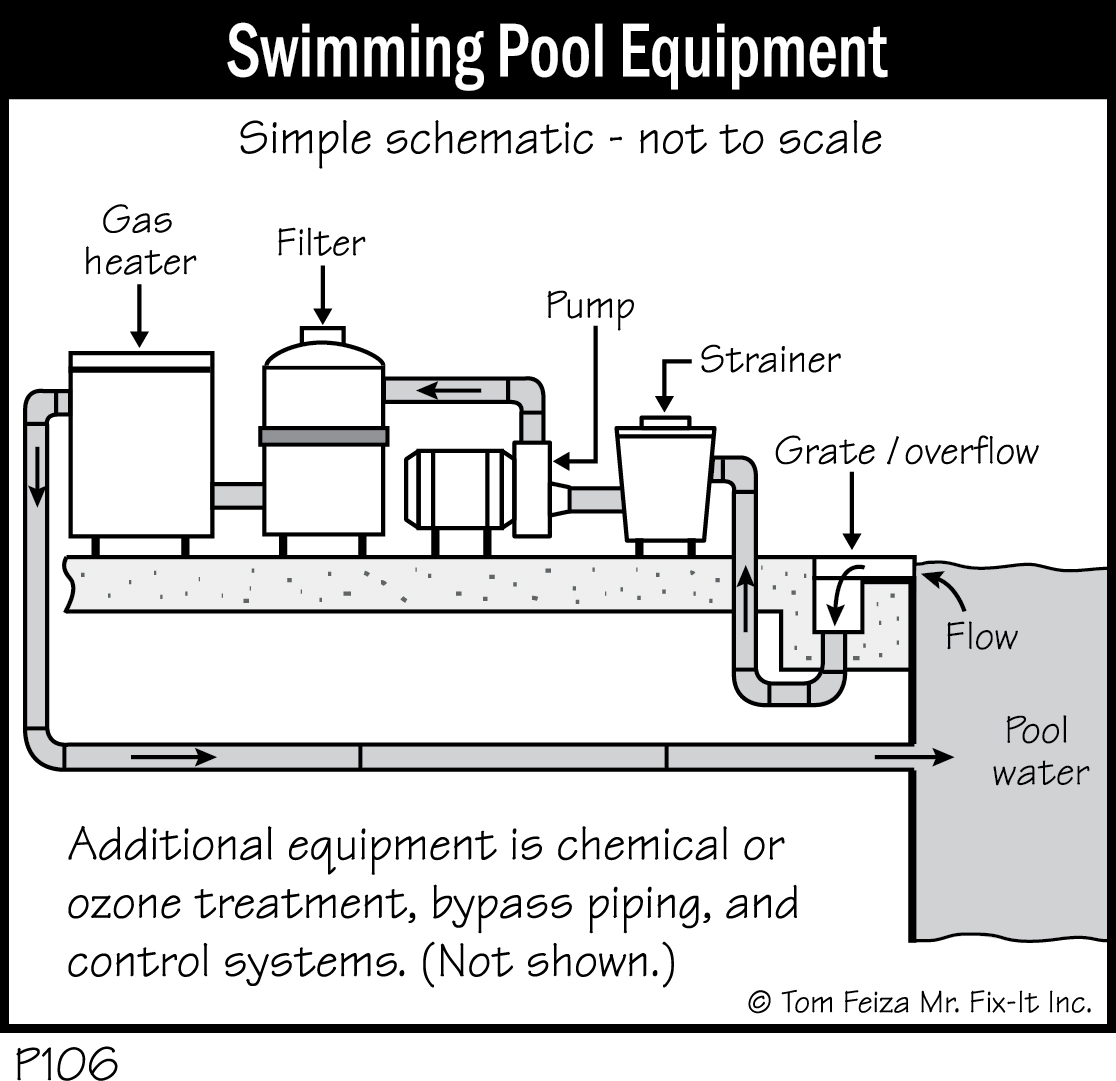
Pools are constructed of poured reinforced concrete, vinyl lined in ground or above ground, or a spray of cement and sand over a metal framework. Some pools are covered with ceramic tile, and some are surrounded with concrete or concrete and tile walking surfaces.
The basic operation of a pool starts with a skimmer and water return lines from the pool. Water from the pool runs through a screen to remove larger debris like leaves and swimming suits (just kidding). From the screen, water is routed through an electrically operated pump and into a filter. After the water is filtered it may be heated, treated, and then returned to the pool through an opening in the side of the pool.
Routine maintenance of the mechanical equipment requires cleaning the screen to remove debris. The filter is replaced, backwashed or cleaned, depending on the type of filter. To perform any maintenance, you must understand how your specific system operates, and you must use valves to turn off or bypass equipment as needed. Often, pool maintenance is best left to professionals. At the least, the homeowner should be trained by a professional and obtain specific operating and maintenance instructions.
Water treatment is required to limit bacteria and keep the water clean. Often, chlorine compounds are used as a disinfectant. It is important to keep the pH of the pool within a certain range so the chlorine remains useful.
Must Know / Must Do Swimming Pool
- Hire a service contractor to routinely check equipment.
- Establish a maintenance routine based on your equipment.
- Treat the water to maintain chemical balance.
- Keep records on maintenance and water chemistry.
- Routinely check for leaks at piping and other systems.
- Regularly change or clean filters and screens.
- Never allow children to use the pool without adults present.
- Use an alarm to alert you to water movement when the pool is not in use.
- Secure the pool with a proper enclosure, and maintain the enclosure.
- Periodically test the GFCI and related safety equipment.
Your pool should be protected by a pool cover. The cover limits evaporation of water and loss of chemicals. It also helps protect the pool from leaves and debris.
Pool Safety
Children must always be supervised when using a swimming pool. It is a good idea to have more than one adult around when using a pool. A fence with locking and self-closing gates should protect the pool. All doors to living areas should be equipped with self-closing hardware and locks at least 54 inches above the floor. An electronic or automated safety monitoring system should be in place to detect water movement when the pool is not in use. A pool cover may also be used for additional safety.
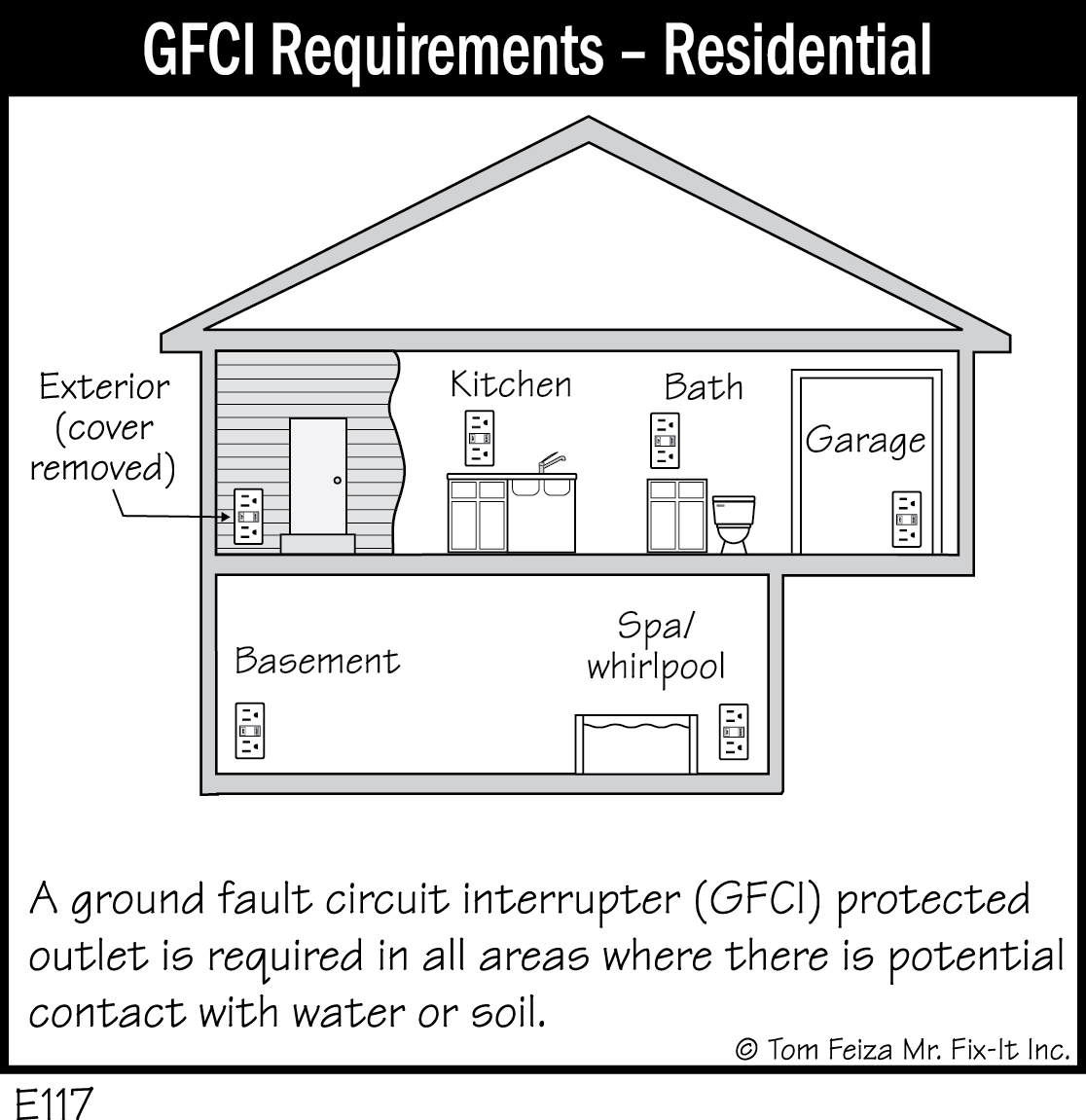
All electrical outlets must be spaced away from the water and be protected by a ground fault circuit interrupter (GFCI). Overhead electrical conductors must be eliminated. All systems must be grounded and bonded. If you have any concerns about the electrical system, have it checked by a qualified electrician.
Pool owners should ensure that all safety requirements of the local municipality and state are followed. You may wish to have the local building inspector check the pool and its equipment for safety. It is a good idea to have a phone near the pool with local emergency assistance numbers next to it.
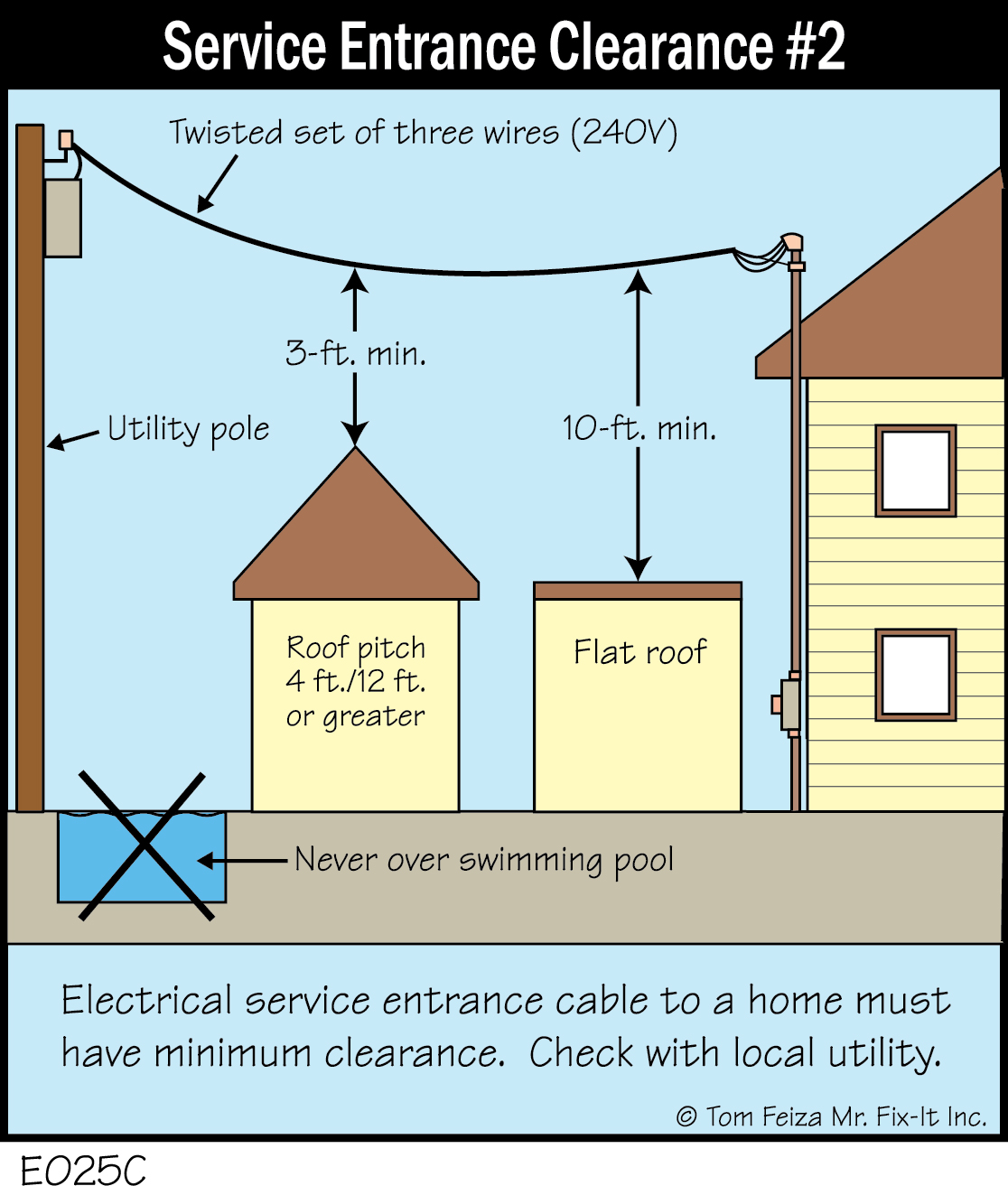
Waterfront Property and Seawalls
Property on lakes and streams must be protected from erosion of soil adjoining the water. This may require some type of retaining wall or rock. Surface water drainage also must be directed around or channeled through any retaining wall to prevent damage. Your local municipality or Department of Natural Resources can provide information on requirements and maintenance.
Property on major bodies of water with wave action may need special protection. Often an engineered and specially constructed seawall is used. Seawalls may consist of poured concrete, steel sheet pile, concrete block, rock or timber. The seawall or bulkhead protects banks by separating the earth or sand behind them from water movement. Provisions must be made to allow surface drainage around or through a seawall.
Generally, seawalls do not protect inland areas from water movement. Your state or municipality can provide local requirements and restrictions for a seawall barrier.